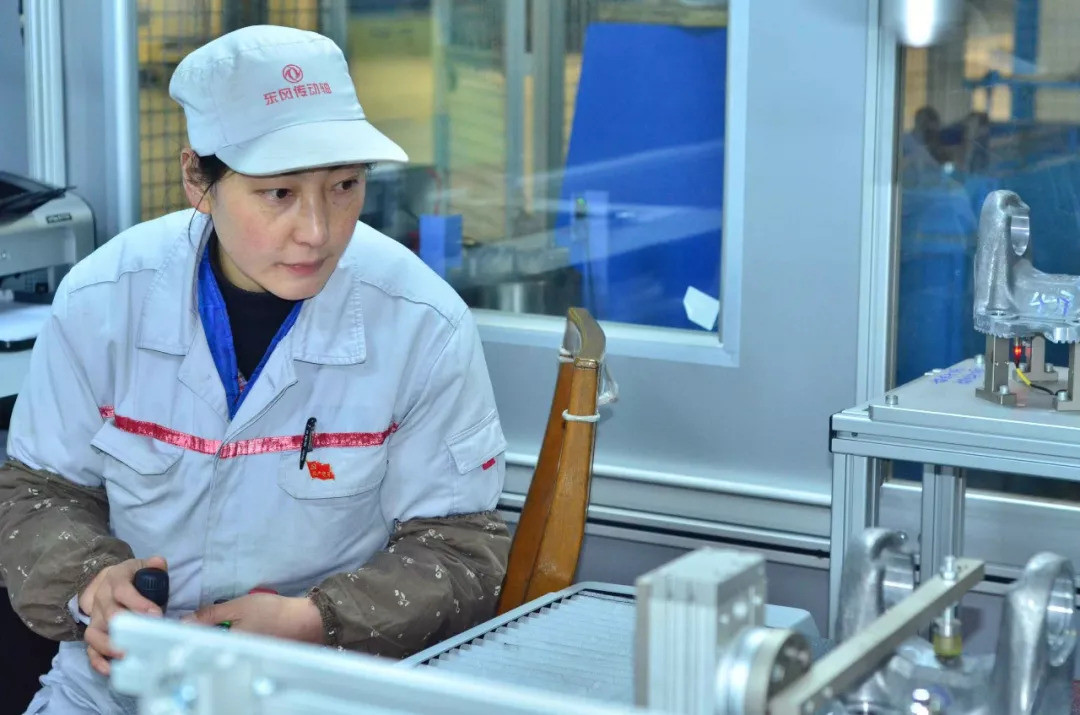
提起这条生产线
朱武梅那是赞不绝口
-高效、省力、品质保障率高……
朱武梅,2017年湖北省“五一劳动奖章”获得者、东风公司劳模。2002年刚来东风传动轴公司时,朱武梅负责加工传动轴突缘叉,当时是采用单机加工的方式,每台机床每天要装夹零件300次,每个零件的重量在4.5公斤左右,而她同时操作三至四台设备,一天下来等于搬运近6吨重量的零件;工作服会被汗水浸湿多次,也会被油污染得又黑又脏,像“黑天鹅”一样。
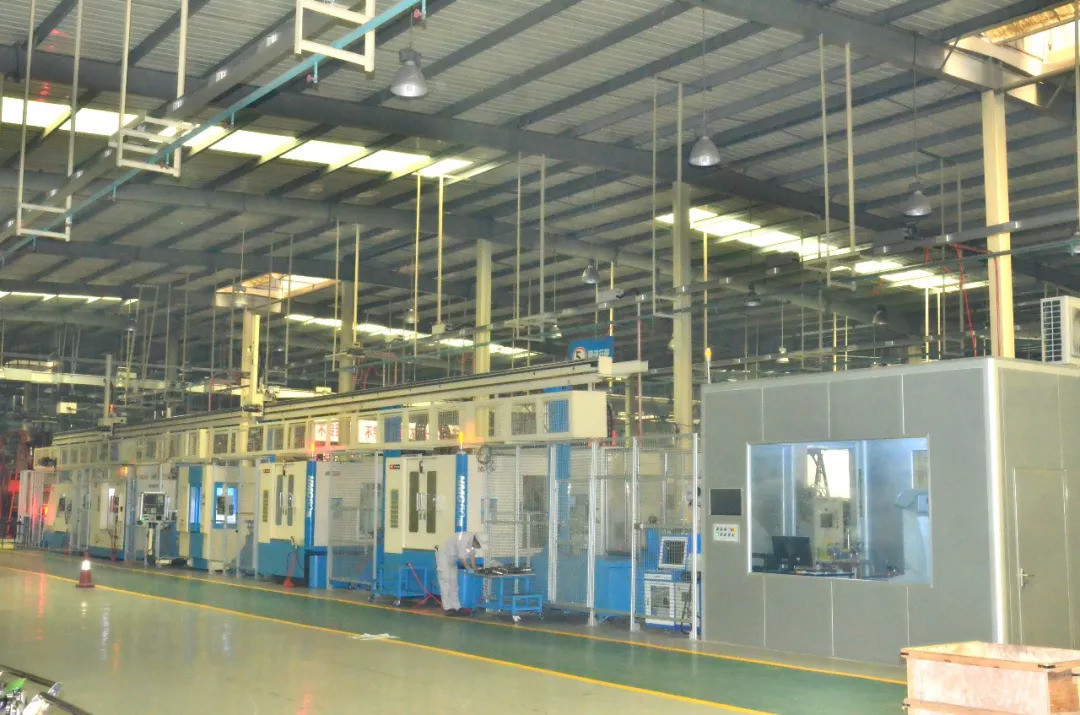
朱武梅介绍,当时工装的颜色是天蓝色,因此也被东风人亲切的称为“蓝精灵”,为了让自己的工装从“黑天鹅”恢复成“蓝精灵”,每天下班后,无论多累,她都要自己动手洗工装。“谁叫咱爱美呢,只能克服劳累洗完衣服再回家了”,朱武梅有些无奈的说到。
“现在她们再也不会像15年前一样,要天天洗工作服了”,负责这条线安装调试的该公司研发首席师刘生好自豪的说到,对于这条生产线,他如数家珍的介绍起来。
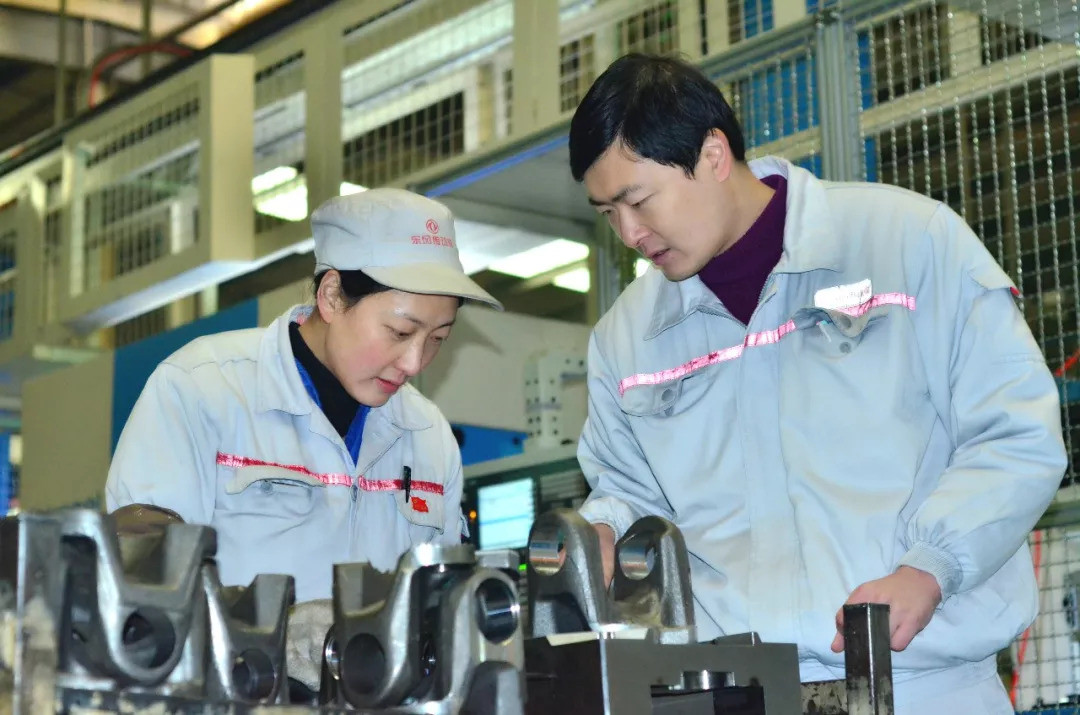
现在朱武梅操作的已经是我们公司生产重型车传动轴零件以来的第四代装备,也是目前在国内屈指可数、十堰地区首条高科技含量的传动轴零件加工生产线。
过去第一代装备就是使用单机加工,靠小车和人工进行搬运的;
第二代使用的是电气自动化的加工线,故障率特别高;
第三代就是数控化,用滑道倒运零件将数控设备连接起来;
第四代就是现在使用的数控自动化装备。
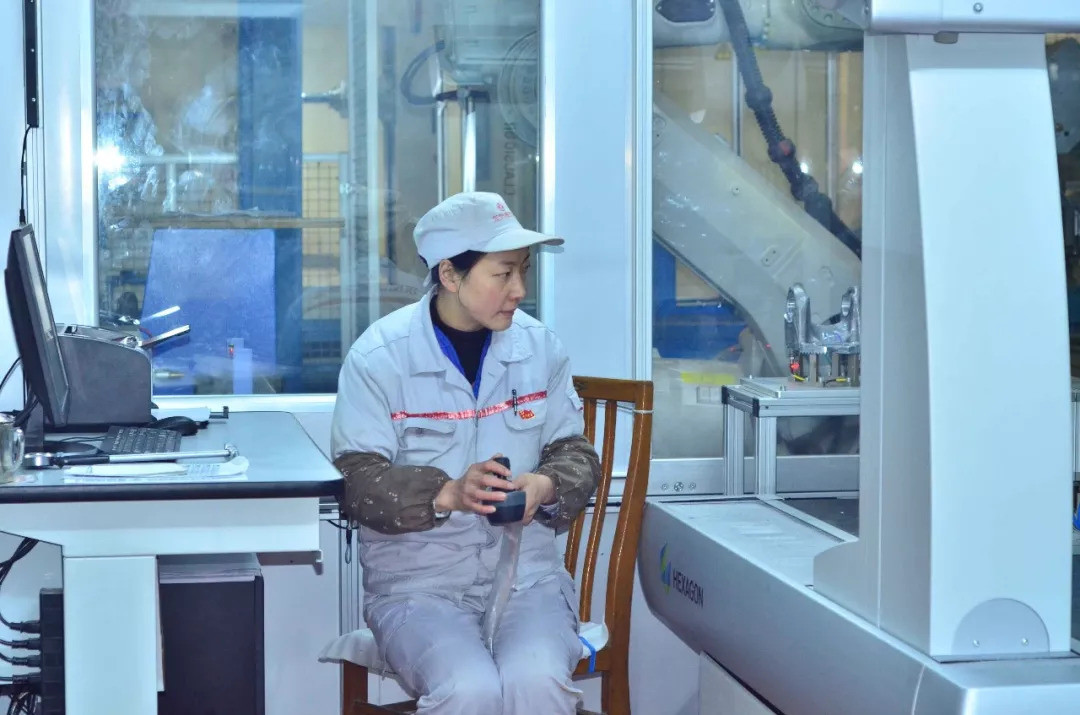
前三种方式劳动强度大,对操作人员的体力消耗都很高,因此工作服特别容易脏,而第四代装备具有整体的工艺先进性,将过去的九台设备的生产线通过优化工艺整合成五台设备的生产线,并且由桁架进行上下料,机器人完成边缘工艺处理、清洗、测量等系列工序,毛坯和产品搬运全部由叉车完成,连加工出来的铁宵都通过电磁力自动吸附到倒运箱中也由叉车倒运,大大降低了员工的劳动强度,不仅如此,整条线还实现了整条线检测自动化,有效消除人为因素,生产线具有的先进工艺还解决了零件加工的变差。
对于未来,刘生好充满豪情的表示,下一步,他的目标是网联化,到那时,操作工可以西装革履的实施零件加工了。